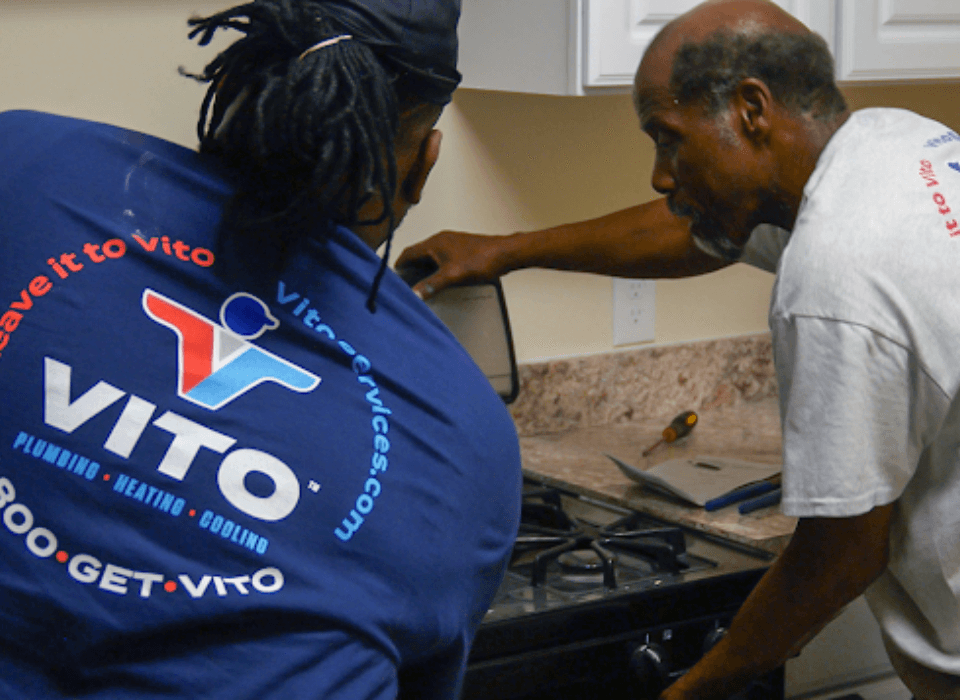
Dependable HVAC & Plumbing Services In Arlington VA
At Vito Services in ArlingtonVA, we take pride in being the leading provider of heating, ventilation, air conditioning (HVAC), plumbing, and air quality management. Our comprehensive range of services includes everything from urgent repairs and precise installations to regular upkeep. Our team, driven by a commitment to excellence, focuses on enhancing the comfort and efficiency of your living spaces.
HVAC Contractor When You Need Help
We ensure your home remains warm in the winter, cool in the summer, and the indoor air quality remains top-notch all year round. Our expertise lies in catering to your specific needs with a dedication to superior service and customer contentment. Choose Vito Services to enjoy the assurance that comes with entrusting your home to Arlington’s most capable hands, and let us improve your living standards for HVAC repair, installation and maintence service because you’re entitled to the best.
Exert Plumbers Serving Arlington 24/7
Need a reliable plumber in Arlington? Whether it’s a leaking pipe, clogged drain, or broken water heater, we’re here to help 24/7. Our licensed plumbing experts offer fast, affordable, and long-lasting repairs—done right the first time.
With decades of experience and fully stocked vans, we handle everything from emergency plumbing services to complete plumbing remodels. No job too small. No stress.
Sewer and Drain Services in Arlington, VA
Blocked drains, backed-up sewers, or strange smells in your home? Our professional drain cleaning in Arlington, includes sewer line repair, camera inspections, and emergency response—getting your pipes flowing again fast. Whether it’s a clogged sink, storm drain, or major underground line, we’re the local plumbing experts to call.
Old and new homes alike deal with drainage issues—especially during storm season. If your toilets are bubbling or your drains smell bad, it’s time to call. We specialise in sewer drain cleaning, drain repair services, and camera-based sewer inspection services. We’ll pinpoint the issue and clear it fast with hydro jet drain cleaning or repair broken lines with minimal disruption. Emergency help available, day or night.
Get the Best Air Conditioning, Heating and Plumbing Service in Arlington
We are excited to welcome you to explore our wealth of positive feedback from our satisfied clients. Every 5-star review reflects the outstanding quality and commitment we invest in each task, regardless of its size. Through these personal experiences, you’ll get a glimpse into what sets Vito apart and the reason why the Arlington VA community relies on us for not only solutions but also for comfort and contentment.
Experience firsthand the excellence and dedication that distinguish us by reviewing these testimonials. Become a part of the Vito family today and discover the remarkable service we pride ourselves on!
Recent Jobs and Reviews in Arlington, VA
Our Local Reviews by City
- Adelphi, MD (3)
- Aldie, VA (1)
- Alexandria, VA (9)
- Arlington, VA (8)
- Ashburn, VA (6)
- Aspen Hill, MD (2)
- Berwyn Heights, MD (1)
- Bethesda, MD (50)
- Bowie, MD (4)
- Boyds, MD (1)
- Brambleton, VA (1)
- Brookeville, MD (1)
- Burke, VA (1)
- Cabin John, MD (1)
- Centreville, VA (5)
- Chantilly, VA (7)
- Chevy Chase, MD (12)
- Clarksburg, MD (1)
- College Park, MD (1)
- Damascus, MD (2)
- Derwood, MD (1)
- Fairfax, VA (17)
- Fairfax Station, VA (3)
- Falls Church, VA (1)
- Fort Washington, MD (4)
- Frederick, MD (2)
- Gaithersburg, MD (18)
- Germantown, MD (8)
- Glenn Dale, MD (1)
- Great Falls, VA (2)
- Haymarket, VA (14)
- Herndon, VA (10)
- Houston, TX (1)
- Hyattsville, MD (3)
- Kensington, MD (4)
- Laytonsville, MD (1)
- Leesburg, VA (1)
- McLean, VA (6)
- Montgomery Village, MD (1)
- North Bethesda, MD (7)
- North Potomac, MD (1)
- Oakton, VA (3)
- Olney, MD (10)
- Poolesville, MD (1)
- Potomac, MD (28)
- Potomac Falls, VA (1)
- Reston, VA (6)
- Rockville, MD (42)
- Silver Spring, MD (58)
- South Riding, VA (1)
- Springfield, VA (1)
- Sterling, VA (3)
- Takoma Park, MD (3)
- Upper Marlboro, MD (1)
- Vienna, VA (4)
- Washington, DC (127)
Job Locations and Reviews
Job Description: tub is leaking through the ceiling / ceiling is open. Arrived at the job site and started making materialist went to pick up my material when I got back started cutting all the pipe that I need to be replaced it and replace everything the way it was supposed to be done once I was done I run water on the tub upstairs, to make sure the tub was really properly and the wasted and overflow was connected properly. Ram water to the sink to make sure the Franco was connected properly too. I was done I cleaned out all my area collecting all my tools and make sure everything was the way it was before I came.
Job Description: 3 garbage disposals not working, one is leaking. Toilet is also leaking at gasket. Arrived at location for 3 garbage disposal not working on each floor and also 2nd floor women bathroom toilet flushmeter was acting up, replaced all 3 garbage disposal tested and clean our mess up as well. The 3rd and 2nd floor are regular 1/2hp garbage disposal but the first floor one was a Serioers 500 1/2 HP. On the second floor we also replaced the p-trap in the same area of the garbage disposal because it was old and the threads were not there anymore. On the second floor women bathroom there were two toilets one in the handicap and the first one walking in. The first one needed a vaccum breaker replacement, checked for leaks no leaks occured. The handicap toilet need a new Diaphram 1.6gpf. All work is done and no leaks occured at this time.
NO AC CALL: checked in the wall magic pack system found bad condenser motor, will have to order part and check warranty CUSTOMER NEED TO TAKE DOWN SHELF THAT HE PUT UP IN FRONT OF THE SYSTEM PICTURES AVAILABLE TO BE BILLED
Reason for plumbing call back: 2 building has no cold water - Arrived at location for no cold water coming out of 104 building 4580. Turn on the water valve for the cold side. Turn on the water and went up to 104 to test and cold water is coming out. Water is back on for that side of the building.
Job Description: tub is leaking through the ceiling / ceiling is open - Arrived at location, Customer said they want to replace waste and over. As inspecting the pipe, it seems old and corroded. Will reschedule for tomorrow morning and replace the whole drain pipe and waste and over flow.
Arrived at location for a leak coming from the ceiling in the gym room area. Went down there and noticed a bubble from the ceiling then also saw a cover to open into. Looked inside and saw that a 3in back steel line was leaking by the coupling. Will have to order parts for this. Customer said it's for hot water only system, so we will be able to come in at anytime and get the problem fix once parts are here. Made a temporary patch to help the leak but this is not a permit repair.
I arrived at my customer home for parts replacement I removed and replaced one three phase blower fan motor check all amps and components and found blower fan motor will run for five minutes over heat shut down and start up when cool off I recommend a replacement of the full system due to age and performance I will provide pricing for replacement of the full system in the morning
Upon arrival, the customer requested maintenance for two systems. I performed maintenance on a 2010 Duel zone with an automatic damper, communicating with the furnace/AC system. I checked all components for proper operation and found no issues. I secured any loose wires and inspected the system for dirt and debris, finding that the blower was slightly dirty and the evaporator coil was very rusty. I also checked the starting components on the condenser unit and found that the capacitor was failing, while the ampered compressor and fan motor were functioning correctly. I found that the coils needed cleaning, and the refrigerant level was good. I also noticed that the condenser was missing a leg and was set up in a tri-pod formation. After performing the necessary maintenance, the system is operational. The second system was a 2010 90% furnace/AC system. I checked all components for proper operation and found no issues. I secured any loose wires and inspected the system for dirt and debr
Estimated To Replace damaged duct and insulate all duck work including new and old ducts
Carrier Infinity 80% Efficiency Furnace Carrier Inverter-Driven Outdoor Condenser Unit Maintenance Work Performed: 1. Carrier Infinity 80% Furnace (Indoor Unit) Inspected and tested all furnace components, including the inducer motor, blower motor, pressure switch, gas valve, ignitor, and control board. All components are operating within manufacturer specifications. Verified communication between the Infinity control system and the furnace — system communicating normally with no fault codes. Checked flue pipe and combustion air intake for blockages or deterioration — all clear and in good condition. Replaced system air filter with new high-efficiency filter. Existing filter showed moderate accumulation of dust and debris. Flushed the EZ Trap condensate drain system to clear any buildup or blockages. Confirmed free-flowing drain to prevent potential water overflow or damage. 2. Carrier Inverter Outdoor Condenser Unit Performed full operational test of the inverter-driven cond
NO AC, OUTDOOR FUSE TRIPPED AND UNIT NOT KEEPING UP. Tenant/owner situation. Carrier heat pump installed in 2023. Upon arrival the tenant advised me that yesterday the 25 amp fuse outside tripped so he replaced it. Once he replaced fuse the unit came on. However today he noticed line set outside was icing up. He had turned system off and kept fan running. When I got there the ice was melted. Before calling for ac I checked the filter, I checked the evaporator coil and found clean, I checked for any oil in the pan at the evap coi and found none. I went to outdoor unit to check all valves and connections to make sure there was no oil. I checked outdoor coil and found clean. I finally called for cooling and the indoor unit kicked on. I felt like set and felt outdoor unit also kicked on. I set thermometer at the return and supply duct and waiting approximately 20 minutes to get a reading and my temp split was 0 degrees. I went to outdoor unit , the compressor and outdoor fan was run
System is a 2016 80% Furnace/AC system. Checked all components for proper operation found no issues with components. Secured any loose wires and checked for dirt and debris. Found blower is clean along with evaporator coil. System does not have an Air Scrubber but does have a Humidifier. Checked condenser unit for proper operation. Checked all starting components found starting components working. Check refrigerant level and found system good. Washed condenser off with water. It's suggested to get a condenser cleaning to prevent the system breaking down. Found capacitor is lower thenFinal cycled system at the time system is operational. Fully checked heating and cooling system. View visual findings from this job at vitoservices.com
A comprehensive inspection and maintenance were carried out on the 2013 Carrier heat pump system to evaluate its performance, identify any system malfunctions, and propose any necessary repairs. The system exhibited several significant issues, as outlined below. Findings: 1. Evaporator Coil Condition The evaporator coil was found to be severely rusted, which suggests a high level of corrosion due to prolonged exposure to moisture and the environment. This rusting is likely to reduce the system's overall efficiency and can cause refrigerant leaks in the long term. The corrosion has compromised the structural integrity of the coil, which could result in failure if left unaddressed. Recommendation: Given the severity of the rust, it may be more cost-effective to replace the entire evaporator coil or even the entire system, as repairing a corroded coil could lead to additional complications in the future. 2. Delta T (Temperature Differential) The temperature differential (Delta T) b
As usual I received excellent service and the technician was knowledgeable and professional and very personable. I am so pleased with this company! Would never use anyone ejse!
WATER LEAK checked for water leak found all water lines, pan and trap ok, water leak is coming from one of the above units and dripping in between the wall and outside of the unit
Replaced ductwork in home
With this option, we will repair Powder Room toilet with new flapper and upstairs recreation bedroom bathroom will require a new fill valve to perform properly. Arrived: Spoke to tenant upon arrival and he gave me his version of what toilets are doing. In powder room toilet, tank doesn't hold water. Inspected tank and flapper adapter is just dangling on flush valve. Adapter was installed with putty. Initial assessment was toilet requires replacement flapper on actual flush valve in aged Sterling toilet. In upstairs recreation room bathroom, tank won't fill up. Bedroom bathroom toilet is operational. Noticed same adapters in all toilets and installed in same manner. In past, I have seen Sterling toilets give difficulty in properly sizing flappers. This could be reasonable excuse for these adapters. Went to truck to communicate with customer. Once reached, made customer aware new toilets are the best option for property. Customer understands and would like estimate sent. Gave customer in
Performing Preventative Maintenance Plumbing Check today. Water pressure in home is 95psig. Excessively high. Water Heater is 5yrs old. Flushed water heater directly into sump pump pit. Sump Pump is fully operational. Flushed water heater in effort to remove sediment buildup and minimize calcification buildup in tank today. Water lines in home are CPVC, which has a maximum pressure rating of 100psig. Main service line is concealed and ¾ in size. Hallway bathroom on main floor of home is in good condition at this time. Upstairs hallway bathroom is in good condition also. Kitchen is in good shape with no leaks present. Performed Water Quality test in kitchen. Chlorine levels are elevated with a reading of 4.4ppm. Hardness levels are Moderately Hard with a reading of 6GPG. Formulated separate proposals for customer approval today and sent via email. Hose bibbs outside are good. Inserted new washer in vacuum breaker for side bibb. With exception of identified concerns, home is in good plum
Checked 2 water coil units. Checked coil, motor, blower wheel and drainage system. Found blowers are good but blower wheels are dirty. Condensation line is clear. Both systems are cooling effectively.
New garage disposal replacement: replaced existing disposal, ran water for 10 minutes to test for proper functionality
Back Flow Prevention Testing: Looking at backflow preventers on site, to judge if they need to be tested or rebuilt
SPRING HVAC CHECK checked filter 16x25x1, checked indoor blower motor and wheel found no ecm motor surge protector, checked condensate pan, line,, pump with no water safety ez trap, checked for uv light system found none, checked for water safeties found condensate pump not wired in, checked return air temperature 68° , checked supply air temperature 55° , checked condenser motor and coil, checked capacitor and contactor, checked all electrical wires and connections, found no surge protector, checked outdoor air temperature 77° checked discharge air temperature 93° , checked liquid line temperature 91, checked suction line temperature 55°
Spring HVAC Maintenance: Client has rescheduled this appointment.
SPRING CHECK WATER FAN COIL checked filter 24x24x1, checked indoor blower motor and wheel, checked uv light system, checked evaporator coil, condesate pan, line, trap, added condesate tablets, checked all electrical wires safeties and connections, checked return air temperature 72° , checked supply air temperature 53°
I arrived at my customer home for a one system AC maintenance outdoor temperature is 65 degrees at this time customer like his/her thermostat set between 65 and 80 degrees in the home I adjusted customer thermostat five degrees below the room temperature in AC mode customer provided all air filters I check all amps and components indoor and outdoor - indoor power input reading 217v, blower fan motor reading 6.8 amps, 24v ez trap and wet switch working, 24v control wires good, indoor control board good, 10kw electric element, blower fan motor needs to be clean, indoor coil needs to be cleaned I flushed indoor drain pipe, 240v contactor burn pitt needed to be replaced , 35+5uf dual capacitor 20uf, defrost board burn need to be replaced before failing, condenser fan motor overheating need to be replaced Daikin ac system working at this time customer will review recommendation and call back when ready.
SPRING CHECK ROOFTOP AC checked filter, checked indoor blower motor and wheel found no ecm motor surge protector, checked condesate Pan line and ez trap, added condesate tablets, checked all water safeties, checked return air temperature 68, checked supply air temperature 52° , checked rooftop AC condenser motor and coil, checked capacitor and contactor, checked all electrical wires and connections, checked outdoor air temperature 54° checked discharge air temperature 63° , checked freon level liquid line temperature 58° , suction line temperature 54°
Great Service! Parris was very friendly and took time to explain what he was doing and made suggestions for being attentive in the future for how the system is working. The coolent in my system is no longer available so if needed, some other product will be required. I understand. He is a very polite and friendly employee.
Hi Elizabeth - We are so glad to hear that you were pleased with Parris' HVAC service. Thank you so much for taking the time to let us know about your experience ... and for the 5-Star Review!
Connor was prompt, super polite, and inspire me with confidence that he could do the job well. He fixed our water heater problem, then came back a week later for another issue. Would highly recommend him and Vita services!
Hi Rachel - We are so glad to hear that you were pleased with Connor's Plumbing service. Thank you so much for taking the time to let us know about your experience, the Recommendation and 5-Star Review!
Fast service, clear communication, and kept a clean work site. 100% satisfied!
Hi Evan - 100% Satisfaction is what we like to hear! Thank you for letting us know about your experience with Vito Services and for the 5-Star Review!
He took the time to explain the problem and how to fix it and even how to make sure the furnace works more efficiently.
Hi Michelle - We are so glad to hear that you were pleased with Danny's HVAC service. Thank you so much for taking the time to let us know about your experience ... and for the 5-Star Review!
Vito is a very good company. We have used their services for many years. Two staffers have been constants: Tracy and Daniel. They are very capable and reliable.
Hi Magdalene - Thank you for the note and 5-Star Review! We will be sure to pass along to Tracy and Daniels 🙂
As usual, good job!
Hi Magdalene - Thank you! We appreciate your business and the 5-Star Review, too:)
Mr George shows up with a great attitude to complete the job.
Thank you, Romeo!