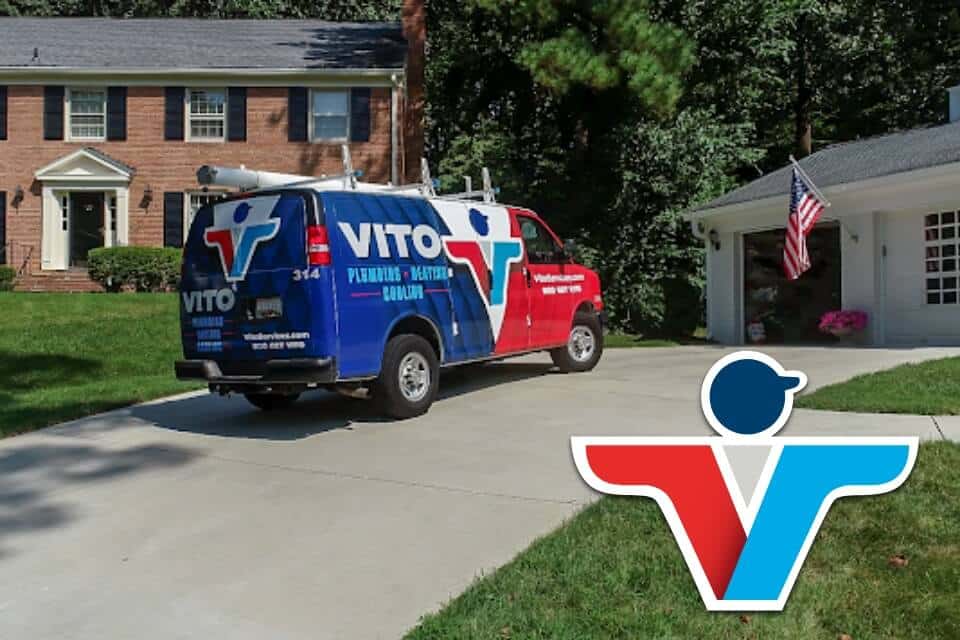
Dependable HVAC & Plumbing Services In Alexandria VA
At Vito Services in Alexandria, we take pride in being the leading provider of heating, ventilation, air conditioning (HVAC), plumbing, and indoor air quality management. Our comprehensive range of services includes everything from urgent repairs and precise installations to regular upkeep.
Our team, driven by a commitment to excellence, focuses on enhancing the comfort and efficiency of your living spaces. We ensure your home remains warm in the winter, cool in the summer, and the air quality remains top-notch all year round.
We also offer plumbing solutions that keep things flowing as they should so your family remains comfortable. Our expertise lies in catering to your specific needs with a dedication to superior service and customer contentment. Choose Vito Services to enjoy the assurance that comes with entrusting your home to Alexandria’s most capable hands, and let us improve your living standards because you’re entitled to the best.
AC Repair Alexandria VA – HVAC Installation & Furnace Services
We handle everything from quick HVAC tune-ups to full system installations. If your system’s underperforming or past its prime, we’ll guide you through the smartest next step—without breaking the bank.
Our HVAC Services Include:
-
Central air conditioning repair
-
Emergency AC service (24/7)
-
HVAC installation & replacement
-
Ductless mini-split systems
-
Smart thermostat setup
-
Seasonal maintenance & tune-ups
-
Energy efficiency upgrades
24/7 Emergency AC Repair
Air conditioning failure doesn’t wait for business hours. That’s why we provide emergency AC repairs 24 hours a day, 7 days a week across all Alexandria zip codes.
Call us if your AC:
-
Blows hot or weak air
-
Makes loud banging, rattling, or buzzing sounds
-
Cycles constantly or won’t shut off
-
Won’t power on at all
-
Leaks water or refrigerant
-
Triggers electrical breakers or unusual smells
We’ll dispatch an experienced HVAC technician fast, diagnose the problem on-site, and get cool air flowing again quickly.
Air Conditioner Installation & Replacement
If your air conditioner is more than 10–15 years old, a new HVAC system can save you money and keep your home more comfortable. We offer expert guidance and seamless installation of:
-
High-efficiency AC units
-
Heat pump systems
-
Ductless cooling solutions
-
Dual-zone temperature control
-
Indoor air quality systems
We handle all permits, inspections, and proper system sizing based on your home’s layout—ensuring lasting results and optimal airflow.
Plumbing Experts You Can Count On in Alexandria
Looking for a reliable plumber in Alexandria, VA? Whether you’re dealing with a clogged drain, leaky pipe, or water heater failure, we’re the team you call when plumbing problems can’t wait. We provide same-day service and emergency plumbing 24/7—because your comfort and safety matter.
From Old Town to Del Ray, we’ve helped homeowners across Alexandria keep their plumbing flowing smoothly. No gimmicks. No delays. Just honest, high-quality work backed by decades of local experience.
Sewer and Drain Services
From Old Town to Del Ray, Alexandria homes can face serious plumbing problems without warning. Our team offers reliable sewer drain cleaning service, sewer pipe inspection, and sewer line repair throughout the area. If your drains are gurgling or backing up, it could be a deeper issue—often solved with sewer drain jet cleaning or targeted sewer repair. Our experienced techs are ready to fix it fast and leave your home as clean as they found it.
Get the Best Cooling, Heating and Plumbing Service in Alexandria
We are excited to welcome you to explore our wealth of positive feedback from our satisfied clients. Every 5-star review reflects the outstanding quality and commitment we invest in each task, regardless of its size. Through these personal experiences, you’ll get a glimpse into what sets Vito apart and the reason why the AlexandriaVA community relies on us for not only solutions but also for comfort and contentment.
Experience firsthand the excellence and dedication that distinguish us by reviewing these testimonials. Become a part of the Vito family today and discover the remarkable service we pride ourselves on!
Recent Jobs and Reviews in Alexandria, VA
Our Local Reviews by City
- Adelphi, MD (3)
- Aldie, VA (1)
- Alexandria, VA (9)
- Arlington, VA (9)
- Ashburn, VA (6)
- Aspen Hill, MD (2)
- Berwyn Heights, MD (1)
- Bethesda, MD (56)
- Bowie, MD (4)
- Boyds, MD (1)
- Brambleton, VA (1)
- Brookeville, MD (1)
- Burke, VA (1)
- Cabin John, MD (1)
- Centreville, VA (5)
- Chantilly, VA (7)
- Chevy Chase, MD (16)
- Chevy Chase Village, MD (1)
- Clarksburg, MD (1)
- Clifton, VA (1)
- College Park, MD (1)
- Damascus, MD (2)
- Derwood, MD (1)
- District Heights, MD (1)
- Fairfax, VA (17)
- Fairfax Station, VA (3)
- Falls Church, VA (1)
- Fort Washington, MD (4)
- Frederick, MD (2)
- Gaithersburg, MD (22)
- Germantown, MD (9)
- Glenn Dale, MD (1)
- Great Falls, VA (2)
- Haymarket, VA (14)
- Herndon, VA (12)
- Houston, TX (1)
- Hyattsville, MD (3)
- Kensington, MD (4)
- Laytonsville, MD (1)
- Leesburg, VA (1)
- McLean, VA (6)
- Montgomery Village, MD (1)
- North Bethesda, MD (8)
- North Potomac, MD (1)
- Oakton, VA (3)
- Olney, MD (10)
- Poolesville, MD (1)
- Potomac, MD (31)
- Potomac Falls, VA (1)
- Reston, VA (7)
- Rockville, MD (43)
- Silver Spring, MD (65)
- South Riding, VA (1)
- Springfield, VA (1)
- Sterling, VA (6)
- Takoma Park, MD (6)
- Upper Marlboro, MD (1)
- Vienna, VA (4)
- Washington, DC (147)
Job Locations and Reviews
Job Description: Customer wants to repair water heater: Arrived onsite, gained entrance to building and knocked on apartment #403. No one answered. Need to bill customer $48 dispatch fee.
replaced floor sink
Arrived on site for a call back to look at a pump under a sink that was leaking and spilling into a pan, looked under the sink and found the pump, ran some troubleshooting for almost an hour involving running lots of water from the sink and dishwasher, taking apart the drain, and inspecting the pump, no weird noises or any leaks of any kind appeared, only solution was to clean out and vacuum the pump pit, ran water again and troubleshooted further for about another 30 min but still never found any leaks or causes for the pump to be having issues, informed customer of findings, cleaned up work area and left
During this maintenance, technician inspected equipment cabinet, wiring,and electrical connections. Check the air flow, air temperature, capacitor, contactor,and fan motor. Inspected blower wheel. Checked condition of refrigerant coils and system duck work. Tested cooling operations and performance. Readabled and confirmed operations. System operations are operating property at this time. I recommend the surge protector ( indoor ECM and outdoor) and Ez trap to help clean the drain line.
Job Description: 2nd floor kitchen drain line needs cleared - Arrived at location to snake 2nd floor kitchen line behind microwave. Ran over 80ft of cable. And pulled back grease and nothing more. There was another sink next to it and it seems like it was backing up but it was filled with trash. Cleaned it and tested as well no leaks occurred at this time.
Arrived on site , customer met with me in the lobby and advised me that underneath their sink is leaking when turning on the facuacet. The customer also advised that the leak happened on Tuesday and they didn’t use the faucet ever since. Once in the kitchen area turned on water and recreate the leak. I observed a 3hp drain pump underneath the sink. I ask the customer was this this drain bucket leaking and overflowing customer agreed. I ran water to see if the pump is still working. After several seconds I can hear the kicking on and dumping water. No leaks. Another person hear on site advised me that the dishwasher was draining and the kitchen sink as running at the same time. I discovered that pump was taking on too much water than it can drain out at a time. I mean the faucet the entire time and the drain pump kicked on approximately 5-6 times through out the time I had the faucet running. No backups or leaks detected. I advised the customer that do not run the kitchen faucet
Looked at job, kitchen line after grease trap is habitually stopping up
Upon arrival at the residence, the customer reported that the air conditioning system was not functioning. Upon inspection, it was observed that the unit was attempting to start but was not fully operating. Further diagnostics revealed a burnt and disconnected wire on the common terminal of the capacitor. The findings were discussed with the customer, and replacement of necessary components was recommended. With the customer’s approval, the contactor and 35/5 capacitor were replaced. The damaged wire was then cut, stripped, and properly reconnected. After all repairs were completed, the system was cycled and is now operational. However, it is important to note that the system is in poor condition overall and will likely require replacement in the near future.
Arrived on site for a callback. I previously came out with the manager to address an issue the customer was having from our last technician's visit. The customer called in again, stating that the drain was not centered. I removed the drain pipe that ties into the basket strainer, as well as the basket strainer itself. I then cleaned the surface area and installed a new basket strainer, applying a new bead of Lexel on both the top and bottom of the strainer. Once tightened down and centered properly, I reconnected the drain pipe. To test for leaks, I filled the sink four times and let it drain. As of ticket completion, no leaks were found. I cleaned up the work area and removed all work-related materials. Thank you for choosing Vito.
Estimate Description: est to replace 5" cast iron pipe. Looked at job to offer estimate
Job Description: Kitchen Sink is backed up - Arrived at location for room 82, kitchen sink was backed up. Removed trap and a lot of water was coming out indicating that the clogged was down the line. Ran snake with k-50 and ran 24ft. Pulled back cable and grabbed nothing back. Put trap back on and filled up sink with cold water. Drain the cold water and no back up occurred. Cleaned up mess and left.
I came out today and extended the condensate line by 3 inches to ensure it would drain properly. The original setup had an improper slope that was causing drainage issues. After making the adjustment, I checked the system to confirm everything was functioning correctly and that the condensate is now draining as it should. If you have any questions or notice any issues, feel free to reach out. I'm always happy to help keep things running smoothly.
Arrived on site with plumbing manager to address a issue the last technician found with the sink when looking we notice it was a good chuck of it that was cut out first removed basket strainer and cleaned up surface of the sink then once cleaned used jb weld to seal in the gap then let dry.after reinstalled basket strainer with lexel and reconnected drain line let customer know to give it till tomorrow use drain cleaned up work area and all work related materials thank you for choosing Vito. Note: per manager 7 1/2 year warranty
Arrived on site, the manager advised me that the station and dish station drains are not draining and are backing up. I advised the customer that the dish station is connect to the hand station so I will snake the line from under the dish station. Went out to my truck to equipment and material to completed and clear the blockage. Went back inside setup equipment and started snaking the drain line. I used 5 cables so I went about 38 ft deep inside of the drain and cleared the blockage. I pulled the cable back and went forward again to insure that any debri or foreign object to break freely from the pipe. Once water cleared i wan water for about 15 min to see if the back reoccurring. No back up. Packed up equipment, cleaned work area and left job site. Thanks for choosing vito 🙂
Pumped All Refrigerant back into condenser then got started on cutting out the old Coil.Came out smooth and Clean and started measuring, New coil was 3 inches bigger so we had to create a new Collar for the ductwork Onsite. New coil went in, no problem. Brazed in, No Problem. Pressurized system at 200psi and held for about 5 mins, then decided to Vacuum and got down to 200 microns. Noticed some of the duct insulation was Very Soaked so went ahead and re-wrapped the duct with new insulation on the underside. Released charge and unit was running very well with a Temp differential of 26°. Wrapped up the work area and left with the unit Running.
Uninstall and remove old garbage disposal. install new 3/4 hp garbage disposal.
Job Description: pipe 1st floor #150 11/2" copper pipe right inside the door. need to bring 10' section of the 11/2" copper pipe. Pipe leak in ceiling
1. 2022 Heat Pump System (Top Floor) 2. 2023 Furnace/AC Split System (Garage with Zoned Dampers) Service Performed: Conducted full maintenance and operational inspection on both HVAC systems. Verified both systems for proper operation and performance. System 1: 2022 Heat Pump – Top Floor Performance: System operating normally with a strong delta T reading, indicating efficient cooling performance. Condensate Line: Successfully flushed to ensure proper drainage. Air Filter: Filter was removed during service and needs to be reinstalled by the customer. Visual Inspection: No signs of refrigerant leaks, corrosion, or abnormal wear. All electrical components and wiring secure. Airflow/Ducting: Airflow within expected range; no apparent obstructions. System 2: 2023 Furnace/AC Split System – Garage Configuration: Split system with three automatic dampers (zoned setup). Performance: System cooling effectively with a good delta T reading. Zoning Check: Dampers functioning correctl
Air Conditioner: Installed 2012 Furnace: Installed 2015 System Type: Split HVAC system Maintenance Performed: Performed full inspection and tune-up of air conditioning system. Cleaned condenser coil with coil cleaner and water rinse. Checked and verified electrical components (capacitor, contactor, relays, etc.). Tested system refrigerant pressures and superheat/subcool to assess system performance. Inspected blower motor, blower wheel, and filter condition. Checked thermostat function and confirmed proper cycling of equipment. Verified drain line was clear and condensate was draining properly. Inspected visible ductwork for air leaks or disconnections. Findings: The evaporator coil is heavily rusted, indicating long-term moisture exposure and potential deterioration of the coil's structural integrity. No active refrigerant leaks were detected during this visit, but due to the visible rust and age of the system, a future leak or system failure is likely. The air conditio
Vito VIP annual service contract renewed, includes 2 HVAC inspections and 1 Plumbing Inspection
WATER LEAK: checked attic air handler found emergency catch pan overflowing without having a water safety switch, removed water from emergency catch pan, cleared blocked drain line checked operation water flowing draining fine
Found emergency drain pan full of water use wet vac to remove water from the pan advice customer that it's going to happen again because there is a hole in the main horizontal drain pan it is on order once we have the pan we will return to replace the horizontal drain pan left customer the small wet vac to vacuum out the water when it fills over the weekend
Service Request: Arrived on site in response to a kitchen washing machine backing up. Removed the drain cover and ran approximately 25–30 feet of cable using my K-50 machine. Initially used a waffle cone head, but encountered resistance around the 20-foot mark. After retrieving the cable, debris including nuts and food waste was present. I then switched to an auger head and was able to run the full length of cable. While removing the snake, I ran and tested the system for approximately five minutes. No backups occurred during this time. The issue was likely caused by a significant buildup of grease and debris in the line. At the time of departure, the system was flowing properly.
Removed old drain pan installed new emergency drain pan new easy trap new float switch re-insulated the existing duct
I arrived at my customer home for the he attic system leak water I vacuumed all the water from the drain pan and recommend the install team to return back out system working at this time. I will provide pricing and proposal for replacement of the garage system
Reliable and knowledgeable
Hi Gloria - "Reliable" and "Knowledgeable" are two words we love to hear in our technician reviews. Thank you for letting us know about your experience with Vito Services and for the 5-Star Review!
Too much time waster time filling a 300-gallon container with a hose smaller than a garden hose driving up customer cost.
Noted, thank you!
I really appreciate Bobby and his ability to deescalate high emotions and concerns from frustration plumbing issues. The way he simplifies explanations is also very helpful for anyone who does not understanding all the technicalities that go in plumbing. I would recommend Bobby to anyone. He gets a 5 star from me. On the contrary, the initial technician who came to diagnose the issue was two hours late from when he said he would arrive. He also gave the wrong recommendation and diagnostic review from my understanding. I would not recommend this guy and suggest he gets more training.
Hi Cannie - We apologize for the inconvenience but glad to hear Bobby was able to take control of the situation. Your note was passed along to our Plumbing Managers, who have addressed this issue. Thank you again for your note.
Good service
Thank you, Cheryl!
Reliable Service and Company
Hi Lesley - Thank you for the 4-Star Review ... please let us know what more we can do next time to earn 5-Stars!
I have three properties which needed to be checked out in preparation for the winter season. As I have a service contract, Vito scheduled me with one technician who came to the first property, then followed me to each of the other two properties, and he thoroughly checked each one, made recommendations, and made sure each one was ready for the heating season. These properties were scattered from one end of norther Virginia to the other, and it was great to be able to do them all on one day, with the same technician. Danny Villalobos was a pro! Very knowledgeable and very helpful! Thank you Danny!
Hi Martha - We couldn't agree more about Danny V! Thank you so much for taking the time to let us know about your experience ... and for the 5-Star Review!
I am grateful that Conor noticed that the installation of my water heater by a previous company was not up to code and that he repaired it for me. He is knowledgeable and courteous.
Hi Pamela - If anyone knows water heater codes, it's Conor! We are so glad he could help, thank you for letting us know and for the 5-Star Review!
Danny was personable and helpful.
Hi Sandy - We are so glad to hear that you were pleased with Danny's HVAC service ... thank you for letting us know and for the 5-Star Review!
I just wanted to express my sincerest gratitude and satisfaction for the outstanding maintenance work Andrew performed on our two air conditioning units. Thank you again for a job exceptionally well done! We look forward to your work and service again.
Gianmarco - We are so glad to hear that you were pleased with Andrew's HVAC work for Vito Services. Thank you for taking the time to let us know and for the 5-Star Review!